Casting Aluminum Mastery: Unleash Your Innovative Prospective
Casting Aluminum Mastery: Unleash Your Innovative Prospective
Blog Article
Unlocking the Potential of Light Weight Aluminum Casting: A Comprehensive Review
Light weight aluminum casting stands as a cornerstone in the world of metalworking, providing a multitude of benefits and applications across different industries. From its historic significance to the modern-day developments in casting strategies, aluminum has actually continuously shown itself as a valuable and flexible product. As we browse with the landscape of aluminum casting procedures and explore the intricacies of high quality control measures, a detailed overview of unlocking real potential of this metal arises. The opportunities seem limitless, promising insights that can revolutionize the method we regard and utilize light weight aluminum in manufacturing (casting aluminum).

History of Light Weight Aluminum Casting
Aluminum spreading has a rich historic background that dates back to old worlds, showcasing the sustaining relevance of this metallurgical process in numerous markets. The origins of aluminum spreading can be traced to around 5,000 B.C. when ancient civilizations like the Egyptians and the Sumerians made use of simple methods to cast little objects. Nevertheless, it was not till the 19th century that aluminum spreading saw significant improvements with the exploration of the Hall-Héroult process for drawing out light weight aluminum from its ore, making it much more obtainable for casting purposes.
The adaptability of light weight aluminum casting enabled for intricate forms and complex styles to be created with precision, further sustaining its fostering across different sectors. Today, light weight aluminum spreading continues to be a cornerstone in the manufacturing of a vast variety of products, highlighting its enduring heritage and value in contemporary manufacturing procedures.
Applications and advantages
With its remarkable strength-to-weight proportion and superb thermal conductivity, aluminum casting uses a myriad of benefits and diverse applications throughout various sectors. One of the main benefits of aluminum casting is its lightweight nature, making it an excellent choice for markets where weight decrease is critical, such as automobile and aerospace.
In terms of applications, light weight aluminum spreading is widely used in the vehicle sector for components like engine blocks, cylinder heads, and wheels due to its strength and lightweight buildings. The versatility of aluminum casting extends to consumer electronics, where it is used in the production of casings and warmth sinks.
Kinds of Light Weight Aluminum Spreading Procedures
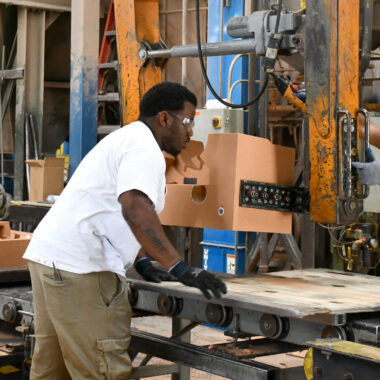
Among the different techniques used in commercial settings, aluminum casting processes include a series of strategies matched to various applications and needs. Among one of the most typical techniques is sand casting, where a mold is created by compacting sand around a pattern of the desired part. This process is versatile and affordable, making it prominent for both little and massive production. Another widely made use of strategy is pass away casting, which involves forcing liquified light weight aluminum into a mold dental caries under high stress. Die casting permits for high precision and repeatability, making it excellent for generating complicated shapes with slim walls. Investment spreading, likewise called lost-wax spreading, is favored for its capacity to create thorough and complex parts with a smooth surface area finish. Last but not browse this site least, long-term mold and mildew casting entails using multiple-use metal mold and mildews to create constant and premium aluminum parts. Each of these light weight aluminum spreading procedures offers distinct benefits, dealing with a wide variety of commercial demands.
Advancements in Light Weight Aluminum Spreading Strategies
Current innovations in aluminum spreading techniques have revolutionized the manufacturing industry, providing enhanced effectiveness and precision in the production of complex components. One noteworthy development is the advancement of 3D sand printing innovation, which allows the development of elaborate sand molds with very little manual work. This technique permits greater layout adaptability and faster manufacturing cycles, making it suitable for prototyping and little batch manufacturing.
In addition, using sophisticated simulation software application has significantly boosted the spreading process this by enabling designers to enhance mold layouts and anticipate prospective defects prior to production starts (casting aluminum). This leads to improved item high quality and decreased product waste
Furthermore, the adoption of vacuum-assisted light weight aluminum casting has actually enhanced the total high quality of castings by lessening porosity and guaranteeing a more uniform circulation of molten steel. This method is specifically helpful for components that call for high architectural honesty and superior surface area finish.
Quality Assurance in Light Weight Aluminum Spreading
The improvements in aluminum casting strategies have not only boosted efficiency and precision yet have likewise underscored the important importance of high quality control in ensuring the dependability and efficiency of actors components. Quality assurance in light weight aluminum casting includes a methodical strategy to examine the manufacturing and check process, determining any type of inconsistencies from established standards that could impact the last item.
One critical aspect of quality control is making use of sophisticated modern technologies such as non-destructive screening approaches like X-ray and ultrasound to detect internal defects without compromising the stability of the why not find out more cast parts. Additionally, executing extensive evaluation procedures at different stages of production helps in identifying and rectifying issues promptly, ensuring that just parts fulfilling the defined requirements are released for use.
Furthermore, top quality control expands past the manufacturing process to incorporate post-casting treatments like warm treatment and surface area ending up, ensuring that the final items fulfill the preferred specifications. By prioritizing quality assurance procedures, producers can enhance item consistency, sturdiness, and overall consumer contentment in the world of aluminum spreading.
Final Thought
Various types of casting procedures and cutting-edge techniques have been created to enhance the efficiency and high quality of light weight aluminum casting. In general, light weight aluminum spreading proceeds to be a valuable manufacturing process with wonderful potential for further improvements in the future.
As we browse via the landscape of light weight aluminum spreading processes and delve into the complexities of high quality control procedures, a thorough overview of unlocking the true potential of this metal emerges. It was not until the 19th century that aluminum casting saw significant advancements with the discovery of the Hall-Héroult process for extracting aluminum from its ore, making it more easily accessible for casting objectives.
Amongst the different techniques utilized in industrial settings, light weight aluminum spreading procedures include a variety of techniques suited to various applications and needs. Financial investment casting, also known as lost-wax spreading, is preferred for its capability to produce detailed and detailed components with a smooth surface coating. Various types of casting procedures and cutting-edge methods have been created to improve the efficiency and quality of light weight aluminum casting.
Report this page